Comprehensive Guide to Effective Product Packaging Maker Repair Methods for Optimal Efficiency
Reliable packaging equipment repair work is crucial for keeping operational continuity and item quality in today's busy production environment. Utilizing an organized method to diagnostics and fixing, alongside preventative upkeep techniques, can dramatically improve equipment long life and performance.
Typical Product Packaging Machine Problems
Product packaging machines, crucial for effective assembly line, typically experience numerous common concerns that can interrupt operations. One prevalent problem is misalignment, which can cause incorrect sealing or labeling, ultimately influencing product honesty and discussion. This imbalance might stem from worn-out components or incorrect configuration throughout first installment.
An additional constant concern is irregular product packaging rates, usually caused by mechanical wear or inadequate upkeep. Irregularity in rate can cause bottlenecks, triggering hold-ups and reducing overall efficiency. Additionally, poor training of employees can exacerbate these concerns, as drivers might not completely understand machine functionalities or repairing methods.
Moreover, product jams are a common occurrence, frequently because of inaccurate material specs or foreign items obstructing the machine's path. Such jams can stop manufacturing, requiring immediate treatment to clear the obstruction and return to procedures.
Lastly, digital faults, including software application glitches or sensing unit failings, can hamper maker functionality - packaging machine repair service. These issues call for prompt interest, as they can result in extended downtime if not addressed quickly. Comprehending these common issues is vital for preserving optimal performance and minimizing disturbances in product packaging procedures
Diagnostic Strategies for Fixings
Applying effective analysis techniques is important for recognizing and resolving problems in packaging equipments. An organized technique to diagnostics allows specialists to identify the origin of breakdowns successfully, therefore lessening downtime and boosting operational effectiveness.
One of the key methods involves aesthetic inspections, where professionals take a look at the equipment for any noticeable signs of wear, damages, or misalignment. This foundational action can typically reveal vital concerns without the demand for advanced tools. Using diagnostic software application can significantly enhance the troubleshooting procedure. These devices analyze equipment performance information, offering insights into abnormalities that may not be immediately noticeable.
An additional crucial strategy is performing practical tests. By methodically operating different components of the machine, specialists can observe efficiency disparities, helping to separate damaged parts. Furthermore, executing vibration evaluation and thermal imaging can uncover concealed issues, such as misaligned belts or overheating bearings, which are commonly precursors to a lot more significant failings.
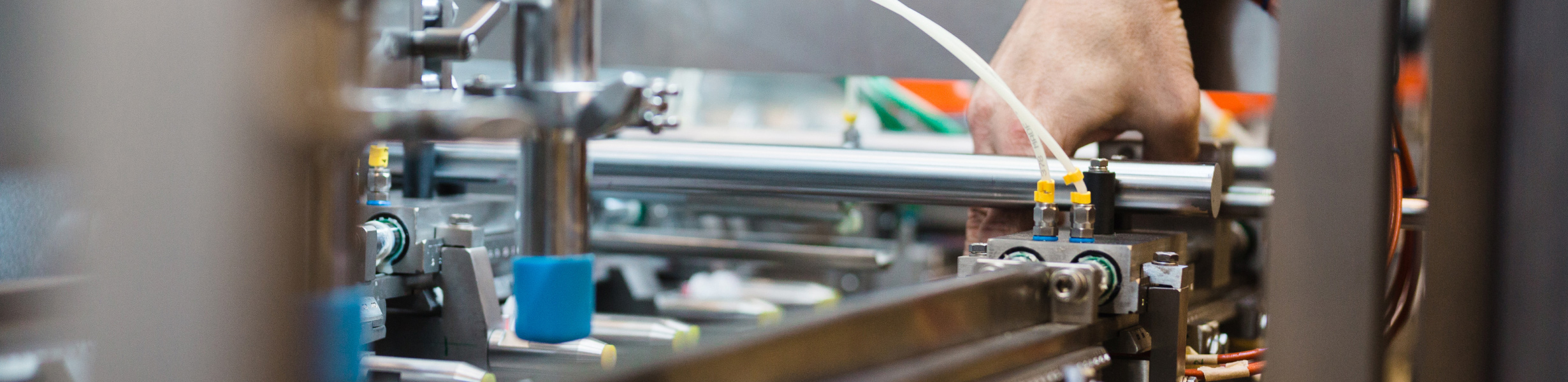
Step-by-Step Repair Work Procedures
A thorough repair service treatment is essential for restoring functionality to malfunctioning packaging equipments. The procedure begins with a comprehensive analysis of the issue, making use of diagnostic methods to determine the source of the breakdown. When recognized, collect the necessary tools and substitute components to help with the repair service.
Next, make certain that the device is powered off and separated from its source of power to ensure safety and security during the fixing. Documenting the equipment's arrangement prior to disassembly can help in reassembly - packaging machine repair service. Carefully get rid of any covers or panels to access the malfunctioning parts, keeping in mind any particular screws or bolts that require interest
Change or fix the defective parts according to the manufacturer's specs, guaranteeing that all connections are safe. After reassembly, carry out an aesthetic evaluation to validate that all components are appropriately installed and that there are no loose links.
As soon as the equipment is rebuilded, reconnect the power and conduct examinations to ensure proper performance. Screen the maker throughout operation to determine any kind of residual concerns. Record the repair service procedure, including components replaced and monitorings, to notify future maintenance efforts. This precise technique advertises ideal see this website device efficiency and durability.
Preventive Maintenance Practices
Preserving the functionality of product packaging devices is not solely dependent on reactive repair treatments; proactive preventative upkeep practices play a substantial role in guaranteeing their durability and efficiency (packaging machine repair service). By carrying out a structured precautionary upkeep program, operators can identify prospective issues prior to they escalate into pricey break downs
Specialists ought to regularly inspect elements such as belts, gears, and sensors for wear and tear. Furthermore, cleansing machines to remove dirt and particles is important for ideal performance and to avoid contamination of products.
Educating personnel on appropriate usage and handling of packaging equipments can additionally decrease the danger of operational mistakes that might cause devices failure. Developing an upkeep routine that includes periodic checks and substitutes of important parts can significantly expand the life-span of the equipment.
Documenting all upkeep activities not just aids in tracking the wellness of the devices but additionally conforms with governing standards. By focusing on preventive maintenance, firms can ensure their packaging equipments operate at peak efficiency, inevitably enhancing efficiency and reducing downtime.
Devices and Resources for Technicians
Equipping professionals with the right tools and resources is essential for efficient packaging maker repair and maintenance. A well-stocked toolkit needs to include accuracy tools such as screwdrivers, calipers, and wrenches tailored for details maker elements. Furthermore, analysis devices like oscilloscopes and multimeters allow specialists to determine electric concerns promptly and properly.
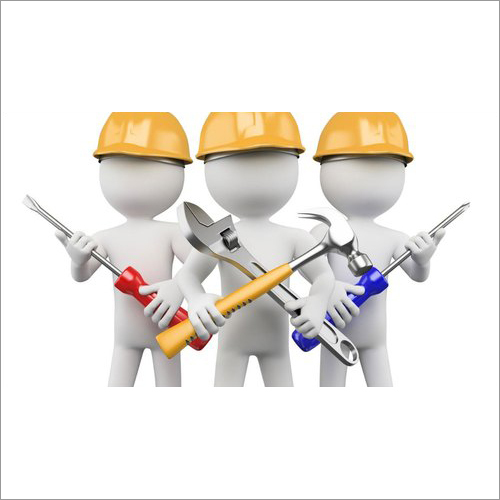
Moreover, purchasing software services for devices monitoring can improve predictive maintenance practices. These applications evaluate device performance information, alerting service technicians to prospective problems before they escalate.
Networking with peers and joining market discussion forums can promote knowledge sharing and best methods amongst professionals, promoting a collaborative environment for constant learning. Keeping connections with suppliers makes certain quick accessibility to spare components and specialized tools, minimizing downtime throughout repair services. By leveraging these resources and devices, service technicians can enhance their performance and performance in keeping ideal performance of product packaging makers.
Conclusion

Efficient packaging device repair service is important for keeping functional continuity and item top quality in today's fast-paced production environment.Product packaging makers, necessary for reliable production lines, typically come across a number of typical issues that can interfere with procedures.A comprehensive repair work procedure is necessary for bring back functionality to malfunctioning packaging makers.Outfitting professionals with the right devices and sources is necessary for reliable packaging machine repair work and upkeep.In verdict, efficient packaging device repair techniques are important for preserving ideal performance and minimizing functional downtime.
Comments on “Packaging Machine Repair Service: Guaranteeing Marginal Downtime and Maximum Effectiveness”